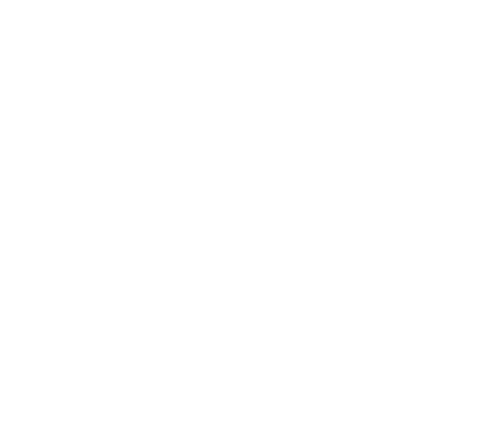
On Behalf of the Flexible Packaging Industry
FPA Monitors Air, Water, and Waste Regulations
Environmental Regulations
Select one of the environmental categories to see how FPA monitors air, water, and waste regulations on behalf of the flexible packaging industry.
Environmental Activity
Quarterly Watch
Environmental Regulatory Index
The Flexible Packaging Association’s (FPA) Environmental Health & Safety Committee (EHS Committee) maintains an Environmental Index online for its members to summarize information on federal environmental laws that could affect flexible packaging manufacturers, and to track FPA’s input into certain regulatory developments. The EHS Index covers federal ambient air quality and hazardous air pollutant standards, solid and hazardous regulations, environmental auditing, and emergency release and public outreach requirements; as well as new source and existing source permitting regulations and implementation. As a general rule, federal environmental standards and permitting rules must be implemented by the states or local agencies once approved by EPA as being consistent and/or “no less stringent” than federal law. The EHS Committee also tracks relevant climate issues such as the recent U.S. bans on industrial and comfort cooling refrigerants (and EPA-approved substitutes); climate issues and litigation; the Federal Trade Commission’s “greenwashing” standards; and the climate disclosure rules such as those recently issued by the Securities and Exchange Commission (now stayed pending judicial review).
To provide new corporate and plant employees with contextual information for regulations that could affect a member’s plants, the Index provides a brief statutory and/or political history for topics. It also indicates the EHS Committee’s input into the regulatory developments either through public comment and/or actual interactions with agency staff. Finally, the FPA Index contains “hot links” to EPA and other agency resources such as agency helplines, online regulatory guidance and libraries, environmental screening maps, and air exposure models, as well as regulatory and judicial references.
The Index is updated quarterly.
Inspect the IndexExpertise on Demand
Environmental Conference Presentations
FPA has compiled a record of all of its presentations to date. See the full list of EHS Committee Meeting presentations and Environmental, Health and Safety Summit presentations.
EHS PresentationsAir Regulations
Terminology
Getting Started
- According to SARA 313, a facility includes "all buildings, equipment, structures, and other stationary items which are located on a single site or contiguous or adjacent sites and which are owned or operated by the same person, or by any person which controls, is controlled by, or under common control with, such person.
- For the purposes of the hazardous waste regulations, it is essential to know the difference between a container and a tank because tanks have more stringent requirements than containers. All hazardous waste generators and transporters, as well as treatment, storage, and disposal facilities should know the difference. A container is any portable device in which a material is stored, transported, treated, disposed of, or otherwise handled. A tank is a stationary device, designed to contain an accumulation of hazardous waste which is constructed primarily of non-earthen materials (e.g., wood, concrete, steel, plastic), which provide structural support.
Collection of Resources
Need to Know
- FPA’s Environmental Health and Safety Committee Plans April 10th Refrigerant Briefing: In addition to its regular update call on April 10, 2024, at 2:00-3:00 p.m. EST, the EHS Committee plans to discuss the EPA’s phase-out of HFCs for refrigerants and other uses under the Paris Treaty and Kigali Amendments to the Montreal Protocol that could impact FPA members’ facilities. FPA members with an interest in this topic are welcome to join the call but will need to contact Emily Patten (epatten@flexpack.com) so that she can arrange for them to join the call.
- Toxics in Packaging Clearinghouse (TPCH) has released its 2009 Assessment of Heavy Metals in Packaging Report. TPCH in its press release said that 14% of retail packaging failed a screening test for toxic heavy metals and are likely in violation of state laws. The results were based on screening 400 packaging samples using x-ray fluorescent analysis. (FOUND AN UPDATE TO THIS REPORT...) 2009 TPCH Report—An Assessment of Heavy Metals in Packaging FPA Comments to EPA on ANPR for Regulating Greenhouse Gases under the Clean Air Act
- The EPA website provides access to a collection of resources with technical information about many areas of air pollution prevention, technology, regulation, measurement, and science.
- Technical Support Document (TSD) for Title V Permitting of Printing and Packaging Facilities: FPA’s Environmental Committee extensively participated in the development of this document and to a large extent is instrumental in getting it to the final stage. While State permitting authorities are not obligated to adhere to this document, EPA’s position is that the approaches included in the document will lead to greater efficiency and effectiveness in issuing Title V permits. Additionally, it will improve the implementation of Title V for printing and packaging facilities and for a wide spectrum of other volatile organic compounds emitters. Please click here to access the document.
- Non-Binding Environmental Guidance Documents: EPA has made available on its website a repository of non-binding general policy, guidance, and interpretive documents that describe how the agency intends to exercise its discretionary authority and explains what a statute or regulation means. Please click here for details.
- EPA’s Office of Compliance has issued National Stack Testing Guidance. The agency has said in the cover letter that this guidance will be treated as interim guidance to provide with an opportunity to evaluate its usage and monitor any potential problems that may arise as individual states apply the provisions. Please let FPA know how this guidance is being implemented by your states and what has been its impact—negative or positive, on your operations. National Stack Testing Transmittal Letter National Stack Testing Guidance
- General Provisions: Don't forget about the General Provisions (40 CFR 63, Subpart A), they also apply if you are subject to any MACT. Here are some useful websites on General Provisions: Rule and Implementation Page
- Estimating Air Emissions: Eastern Research Group has prepared guidelines describing preferred and alternative methods for estimating air emissions from the printing, packaging, and graphic arts industry. This consensus document has been furnished to EPA but has not been reviewed/approved by the Agency at this point. Please click here to access the document.
Water Regulations
Terminology & Record Keeping
NEED TO KNOW
- Wastewater Definition: Wastewater is defined as hazardous waste that contains less than one percent by weight total organic carbon and less than one percent by weight total suspended solids. Nonwastewater is any hazardous waste that does not meet the criteria for wastewater. These definitions are essential for determining which hazardous waste treatability group and treatment standards are applicable. For wastewaters, concentration-based treatment standards are typically higher for nonwastewaters than for wastewaters. Please click here for more information.
- How Long Are You Required to Retain Monitoring Records, Copies of Reports, and Any Other Paperwork Affiliated With Your Facility's Storm Water Permit? According to 40 CFR 122.41(j), all records must be retained for at least 3 years. This record-keeping requirement may be extended at the permitting authority's discretion.
Waste Regulations
General Information
NEED TO KNOW
- Conflict Minerals Rule: Litigation Update: On August 22, 2012 the U.S Securities and Exchange Commission issued the “Conflict Minerals Rule” mandated by the 2010 Dodd-Frank Wall Street Reform & Consumer protection Act. The Rule requires that if conflict minerals (tin, tantalum, tungsten or gold; abbreviated as 3TG) are necessary to the functionality or production of products manufactured or contracted to be manufactured by an SEC reporting company, the company must perform due diligence and make specified disclosures as to the source of the 3TG in its reportable products. The compliance reporting period began January 1, 2013, and the first reports are due to be filed on June 2, 2014. Please click here for more information.
- How DOT Assesses Civil Penalties: There are two methods outlined for assessing civil penalties in the hazardous materials regulations: tickets and notices of violation. Please click here for details.
- What is DOT Empty? Please click here for information.
Workplace Safety
PREPARE YOUR STAFF
- HAZWOPER Chain of Command: The organizational structure part of the site program must establish the specific chain of command and specify the overall responsibilities of supervisors and employees. Please click here for details.
- DOT Hazmat Training Recordkeeping Requirements: Records must be retained for each hazmat employee for as long as the employee is employed by the hazmat employer and for 90 days after termination of employment as a hazmat employee. Please click here for details.
- Hazmat Employees Must Receive Training: According to the DOT regulations, a hazmat employee is a person who is employed by a hazmat employer and who in the course of their employment directly affects hazardous materials transportation safety. For more information,please click here.
- Emergency Response Guidebook: The Emergency Response Guidebook (ERG) is a guide designed to assist responders with identification of the hazards of a material during incidents so that they can protect themselves and the public during response activities. Transportation authorities from the US, Canada and Mexico developed the ERG and update it regularly. It is revised and reissued every three or four years. Please click here for details.
- Hazardous Waste Inspector's Checklist: If a RCRA inspector was waiting in the lobby right now, would you be ready? The Vermont Waste Management Division has published the checklist used by its enforcement personnel when conducting inspections. The checklist is helpful to hazardous waste generators in Vermont or any other state to use as a self-audit tool. For a copy of the checklist, please click here.
- EPA Notification When Changing Hazardous Waste Contact Person: With few exceptions, every hazardous waste generator, transporter, and facility that treats, stores, or disposes of hazardous waste must have an EPA identification number. This number is obtained through the submission of EPA Form 8700-12 which requires, in part, the name and telephone number of a facility contact. EPA requires the form to be updated whenever there is a change in the facility contact information. Other conditions requiring an update to the form are listed in the Form 8700-12 instruction booklet. Standards Applicable to Generators of Hazardous Waste
Labeling Requirements
PREPARE YOUR PRODUCT
- Hazard Communication: Hazard Warnings: All containers of hazardous chemicals covered under OSHA's Hazard Communication standard must be labeled with an appropriate "hazard warning." For more information, please click here. To determine the physical and health hazards which must be identified by these appropriate “hazard warnings,” see the definitions for “physical hazard” and “health hazard," please click here. Relevant Interpretations
- Hazard Communication Requirements for Articles: Under OSHA's Hazard Communication Standard, items meeting the definition of an article are not considered to be hazardous chemicals and are therefore not subject to the regulation. Please click here for information. OSHA’s definition of an article. Interpretations
Plans & Requirements
MANAGING YOUR WASTE
- Hazmat Security Plan: On March 25, 2003, the Research and Special Programs Administration (RSPA) issued security requirements for shippers and carriers of hazardous materials. The new security requirements have created two new major responsibilities. For more information, please click here.
- UST Corrective Action Plans: An underground storage tank (UST) corrective action plan may be required by your state implementing agency if there is a likelihood that a release from the UST could result in a high risk to human health and the environment in the UST area. Please click here for details.
- Unmanifested Waste Reports: Normally, all of the hazardous wastes accepted by a hazardous waste treatment, storage, or disposal facility (TSD) are accompanied by a hazardous waste manifest. What should the TSD do if they accept a hazardous waste that was not accompanied by a manifest? Please click here for details.
- Lead Acid Battery Marking Requirements: Lead-acid batteries intended to be reclaimed are exempt from nearly all hazardous waste requirements, including the satellite and accumulation point container marking requirements, and those for universal wastes. Because some states have requirements that are more restrictive that the federal standards, state regulations for lead-acid batteries should be reviewed to confirm the applicability of this exemption in your state. For more information, please click here.
- What is A DOT Material of Trade and Why is it Important? DOT allows for some otherwise fully regulated hazardous materials to be transported in commerce without being subject to the requirements of the hazardous materials regulations as long as certain conditions are met. Please click here for information.
- When Does Flammable Parts Washer Solvent Become Hazardous Waste? During the period in which parts washer is functioning as a process unit, and any waste that may be generated while the parts washer is functioning is exempt under 40 CFR 261.4(c). This regulation concludes with the two conditions under which the exemption no longer applies: as soon as the solvent is removed from the parts washer, or after it remains in a non-operating unit for more than 90 days. Consequently, the solvent becomes a hazardous waste the moment it is removed or replaced, or the moment after which the parts washer has been unused for 90 days.
- Hazardous Material Shipping Paper Retention Rule Amended: DOT’s Research and Special Projects Administration has amended the Hazardous Materials Regulations to require shippers and carriers to retain shipping papers, or an electronic image thereof, for a period of 375 days after the date the hazardous material is accepted by the carrier. The previous requirement for retention was one year. Please click here for full details.
Understanding the Table
HAZARDOUS MATERIALS TABLE
- What Does it Mean When the Letter "I" is in Column 1 of the Hazardous Materials Table? The symbol "I" in Column 1 of the Hazardous Materials Table (HMT) identifies the proper shipping names that are appropriate for use when describing materials intended for international transport. A different proper shipping name must be used when domestic transportation is involved for that material. For example, Sulfur, 4.1, UN1350, III would be appropriate for international shipments of sulfur. For shipments of sulfur by ground within the U.S., the appropriate basic shipping description is Sulfur, 9, NA1350, III.
- What Does it Mean When the Letter "G" is in Column 1 of the Hazardous Materials Table? The letter "G" in Column 1 of the Hazardous Materials Table (HMT) indicates that proper shipping names with this designation be supplemented with the technical name(s) of the hazardous materials in association with the basic description; for example; Corrosive liquid, n.o.s., (caprylyl chloride). When more than one substance contributes to the hazardous nature of the material, at least two technical names must be listed; for example; Corrosive liquids, n.o.s., (sodium hydroxide, potassium hydroxide).
- What Does It Mean When the Letter "D" is in Column 1 of the Hazardous Materials Table? The letter "D" in Column 1 of the Hazardous Materials Table (HMT) indicates that the associated proper shipping name is appropriate to use when shipping that material domestically, but it may be inappropriate for use in international transportation under the international, air, and vessel regulations. Shippers may have to choose another proper shipping name when international transportation is involved. For example, Diesel fuel, NA 1993 is a proper shipping name recognized by DOT for domestic transportation, but the entry appropriate for international transportation is Diesel fuel, UN 1202.